|
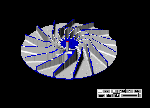
SolidSurfacer is an option to Virtual Gibbs Mill for importing, creating and machining solid and surface parts. Completely integrated into Virtual Gibbs, SolidSurfacer provides a single, interactive programming environment. It is ideal for programming a wide range of 2 and 3-axis parts, including mold cavities, cores, base plates, dies, and aerospace, medical and automotive components. SolidSurfacer uses the latest solid modeling technology, directly reading and machining the solid models of many different CAD systems. Combining this technology with Virtual Gibbs’ graphic interface, cut-part rendering, associativity and full suite of standard mill features, SolidSurfacer provides incredible power and productivity for complex part programming.
Machine Solids from Many CAD Sources
Directly machine solid models from virtually any source, including Parasolid files, SAT files and many others.
Import, Repair and Machine IGES Surface Files
Import and machine IGES trimmed NURB surfaces from any CAD source. Specialized tools are provided for the import, repair and automatic solidification of IGES files.
Create Solid Models
Use the integrated solid and surface modeling capabilities to build your own solid and surface part models, directly from blueprint geometry, imported IGES or DXF geometry or other solid models.
Create Efficient Part Programs
Integrated advanced machining capabilities create ultra-efficient toolpaths, including highly automatic multi-tool, multi-surface roughing and finishing, gouge-free toolpaths and “material only” machining.
Why Is Associativity Important?
The entire Virtual Gibbs CAM product line is built with one primary objective– ease of use. Associativity is an important part of that, as it allows you to make changes to your part file and all affected aspects of the part update automatically. All types of changes– tooling, geometry, machining parameters– are completely incorporated into the part with one simple mouse click. This gives you the freedom to experiment, build new parts from similar existing parts and create families-of-parts quickly and easily.
|
Model Creation
Solid and Surface Modeling
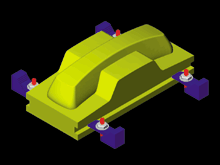
• NURBS-based solid and surface models
• Interactive object-based interface
• Full associativity for quick and easy changes
• Solid model history to track and change part creation
• Fast rendering of surfaces and solid models
• Boolean functions of any two bodies: Union (add), Difference (subtract) and Intersection
• Automatic corner rounding and chamfering
• Variable radius blending
• Solidify surfaces into solid bodies
• Slice and section a body
• Offset and shell a body
• Create parting line curve
• Draft a body
• Automatic core and cavity creation
• Atomic body creation, including:
- Sphere
- Cuboid (blocks, rectangular solids)
- Extruded shape with taper
- Revolved shape
- Lofted NURB solids through multiple shapes
- Swept NURB solids through multiple shapes/drive curves
• Local editing of solids
• Provide for shrinkage factors
• Make a body a part, a fixture or the stock material
• Properties calculations, including surface area, volume and periphery
• IGES import, repair and automatic solidification
• Surface creation functions include:
- Plane
- Revolved shape
- Lofted NURB surfaces through multiple shapes
- Swept NURB surfaces through multiple shapes
- Trimmed planes
- Trim/untrim surface
- Intersect surfaces
- Create surface from selected body face
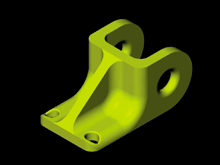
Solid Model Formats Read
• Parasolid® files, including Unigraphics®, SolidWorks®, Intergraph SolidEdge®, Bentley MicroStation Modeler® and ComputerVision DesignWave®
• ACIS® SAT files, including AutoCAD Designer®, Intergraph SolidEdge®, Bentley MicroStation Modeler®, Applicon Bravo®, Hewlett-Packard’s CoCreate® and many others
• Future solid model formats include ProEngineer®, PT Modeler®, Catia®, STEP and others
IGES Entities Imported
• All 2D and 3D wireframe geometry elements
• Surface entities: 108 - Plane, 114 - Parametric surface,
118 - Ruled surface, 120 - Surface of revolution, 122 -Tab cylinder,
128 - Rational B-Spline surface (NURB), 140 - Offset surface,
143 - Bounded surface, 144 - Trimmed parametric surface
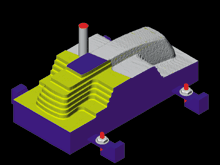
Machining
General
• Fast, gouge-free toolpaths over multiple surfaces and/or complex bodies
• Apply multiple tools to multiple surfaces in a single step
• Full associativity to update all changes throughout the entire part
• Optimization of toolpaths into G17, G18, G19 arcs, useful for constant Z roughing
• Machine from complex 3D stock bodies, with “material only” cutting
• Automatic fixture avoidance
• Support for ballnose, bullnose and flat endmills
• Constant and variable cut width
• Automatic 2D optimization of pocketing and contouring toolpaths for 2 and 2.5D bodies
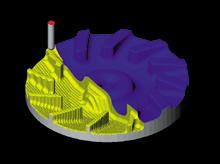
Roughing
• Spiral-out roughing with constant Z steps
• Single-axis lace cutting, including single direction, back and forth, user specified angle with constant Z steps, offset Z, variable offset Z, constant number of passes over the entire model and optional automatic periphery cleanup
• Smart drilling of entry holes in multi-level pockets
• Hit Z flats option for pocketing
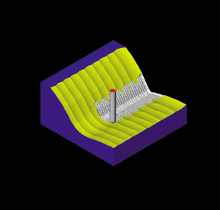
Finishing
• Constant Z depth or constant scallop/ridge height finishing passes
• Lace cut finishing, including single axis, single direction, back and forth and user specified angle
• Clean-up only large ridge areas left by previous lace cut at a different angle
• Clean-up only concave fillets left by a previous larger radius tool (corner clean-up/rest milling)
• Finish top surfaces and clean-up ridge areas left by previous constant Z roughing
• Cut entire selected areas
• Automatic intersection machining following clean-up from previous tools (pencil milling)
• Multi-surface flow machining
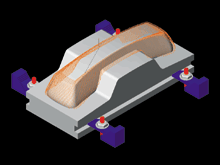
Other Functions
• Projection of toolpaths on multi-surface parts
• User control of stock amounts and cutting tolerances
• User definable constraint shapes, surfaces and solids
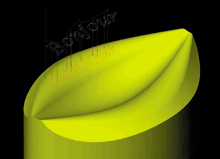
Post Processors
• Uses Gibbs library of over 2,000 proven post processors.
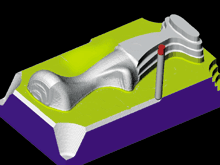
Operating Systems
• Available for Windows® 95/98 NT/ WIN2000 and XP.
Request A Quote |
|